Summary:
The Future of Manufacturing: Innovations in Automating material handling
What is Automating Material Handling?
Eco-Friendly Approaches in Bulk Material Conveying
What are the components that make up an Bulk Material Conveying?
Benefits of Robotic Material Handling
Applications of Robotics in Material Handling
Technological Advancements Driving Innovation in Robotics
What is Automating Material Handling?
Automating material handling refers to the process of using automated systems, machinery, and technology to streamline and optimize the movement, storage, and control of materials within a manufacturing or distribution environment. This involves replacing manual labor and traditional material handling methods with automated solutions to improve efficiency, accuracy, safety, and overall productivity.
Automating material handling can include various technologies such as conveyor systems, robotic arms, automated guided vehicles (AGVs), automated storage and retrieval systems (AS/RS), and warehouse management systems (WMS) integrated with advanced software and sensors. These technologies work together to perform tasks such as picking, packing, sorting, transporting, and storing materials with minimal human intervention.
The goal of automating material handling is to reduce operational costs, enhance workflow efficiency, increase throughput, ensure accuracy in inventory management, and create a safer working environment by minimizing the risk of accidents and injuries associated with manual material handling. It also enables businesses to adapt to changing demands and market trends more effectively while improving overall customer satisfaction.
Eco-Friendly Approaches in Bulk Material Conveying
Sustainable Material Selection
Utilizing Recycled and Renewable Materials in Conveyor Construction
Minimizing Environmental Impact through Responsible Sourcing Practices
Benefits of Sustainable Materials for Long-Term Operations
Energy-Efficient Conveyance Systems
Implementing High-Efficiency Motors and Drives
Optimizing Conveyor Layouts for Reduced Energy Consumption
Incorporating Regenerative Braking and Energy Recovery Systems
Emission Reduction Strategies
Transitioning to Electric-Powered Conveyors
Integration of Low-Emission Technologies in Conveying Equipment
Monitoring and Mitigating Air Pollutants from Conveyance Processes
Waste Reduction and Recycling
Implementing Material Recovery Systems along Conveyors
Encouraging Closed-Loop Material Handling Practices
Minimizing Packaging Waste through Efficient Conveyance
Environmental Compliance and Certification
Meeting Regulatory Standards for Environmental Protection
Obtaining Eco-Friendly Certifications for Conveyance Systems
Continuous Improvement Strategies for Sustainable Operations
What are the components that make up an Bulk Material Conveying?
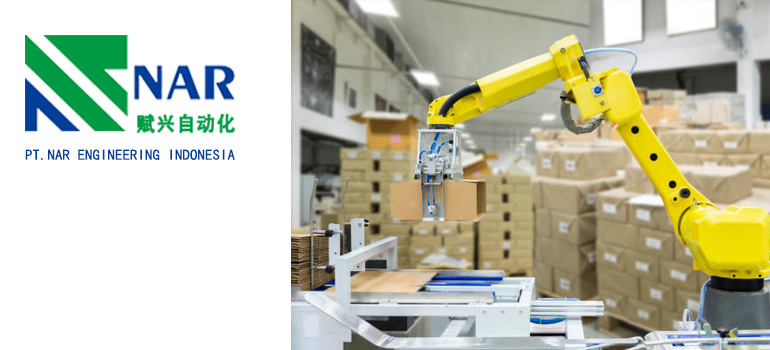
Manipulator Arm
The mechanical arm responsible for performing tasks such as picking, placing, and manipulating objects.
Functionality: Utilizes joints, links, and end-effectors to carry out precise movements and actions.
End-Effector
The tool or attachment at the end of the manipulator arm designed for specific tasks.
Functionality: Various end-effectors include grippers, suction cups, and specialized tools tailored to the application requirements.
Sensors and Perception Systems
Devices used to gather information about the robot’s environment.
Functionality: Includes cameras, LiDAR, proximity sensors, and tactile sensors for object detection, localization, and navigation.
Control System
Software and hardware components that govern the operation of the robot.
Functionality: Coordinates motion, manages task execution, and ensures safety through programming and real-time feedback.
Power and Actuation
Systems responsible for providing energy and converting it into mechanical motion.
Functionality: Includes motors, actuators, and power sources (electric, hydraulic, pneumatic) to drive the robot’s movements and functions.
Communication Interface
Interfaces enabling communication between the robot and external systems.
Functionality: Facilitates integration with other machinery, sensors, and control systems for coordinated operations and data exchange.
Programming and Control Software
Software tools used to program and control the robot’s behavior.
Functionality: Allows users to define tasks, trajectories, and behaviors, as well as to monitor and adjust operation parameters.
Benefits of Robotic Material Handling
Increased Efficiency and Productivity
Robotic material handling systems can operate continuously and consistently without fatigue, leading to higher throughput and reduced cycle times.
Tasks such as picking, packing, and sorting can be performed at a faster pace, optimizing overall workflow efficiency.
Improved Accuracy and Quality Control
Robots are capable of precise and repeatable movements, resulting in more accurate handling of materials and products.
Automation reduces the risk of human error, ensuring consistency in product quality and minimizing defects.
Enhanced Safety for Workers and Products
By automating hazardous or physically demanding tasks, robotic material handling systems help minimize the risk of workplace injuries and accidents.
Advanced safety features such as collision detection and force-limiting technology ensure safe interaction between robots and human operators.
Flexibility and Adaptability
Robotic systems can be reprogrammed and reconfigured to accommodate changes in production requirements or product specifications.
Modular designs and interchangeable end-effectors enable robots to handle a wide range of materials and products with minimal downtime.
Cost Savings and Return on Investment (ROI)
While the initial investment in robotic material handling systems may be significant, the long-term cost savings from increased efficiency, reduced labor costs, and improved resource utilization can result in a favorable ROI.
Automation allows businesses to reallocate human resources to more value-added tasks, optimizing overall operational costs.
Scalability and Future-Proofing
Robotic material handling systems can scale according to the evolving needs of a business, from small-scale operations to large-scale production facilities.
Continuous advancements in robotics technology ensure that investments in automation remain relevant and adaptable to future industry trends and challenges.
Applications of Robotics in Material Handling
Automated Picking and Packing
E-commerce Fulfillment Centers: Robots are used to pick items from shelves and pack them into shipping containers, increasing order accuracy and fulfillment speed.
Distribution Warehouses: Robots handle the sorting and packing of goods for distribution, optimizing inventory management and order processing.
Sorting and Distribution
Parcel Sorting Centers: Robotic sorting systems classify packages based on destination, size, and weight, streamlining the distribution process and reducing sorting errors.
Airport Baggage Handling: Robots transport luggage between terminals and flights, ensuring efficient baggage routing and minimizing travel delays.
Assembly Line Automation
Automotive Manufacturing: Robots assemble components and perform tasks such as welding, painting, and quality inspection on automotive assembly lines, improving production efficiency and product quality.
Electronics Manufacturing: Robots handle delicate electronic components and perform intricate assembly tasks with precision and speed, reducing manufacturing defects and rework.
Material Transfer and Conveyance
Logistics and Transportation: Automated guided vehicles (AGVs) and autonomous mobile robots (AMRs) transport materials and goods within warehouses, factories, and distribution centers, optimizing material flow and resource utilization.
Bulk Material Handling: Robots are used in industries such as mining, construction, and agriculture to transport and manipulate bulk materials such as ores, aggregates, and grains, improving operational efficiency and worker safety.
Packaging and Palletizing
Food and Beverage Industry: Robots package food products into containers, seal packages, and palletize finished goods for shipment, ensuring compliance with hygiene standards and maximizing packaging efficiency.
Consumer Goods Manufacturing: Robots palletize finished products onto shipping pallets, optimizing warehouse space and reducing labor costs associated with manual palletizing.
Technological Advancements Driving Innovation in Robotics
Artificial Intelligence (AI) and Machine Learning
Advanced Perception: AI algorithms enable robots to interpret complex sensory data from cameras, LiDAR, and other sensors, improving object recognition and navigation capabilities.
Autonomous Decision-Making: Machine learning algorithms allow robots to adapt their behavior based on environmental changes and past experiences, enhancing their ability to handle dynamic and unstructured environments.
Sensor Technology
Multi-Sensor Fusion: Integration of multiple sensors, including vision, proximity, and force sensors, provides robots with comprehensive situational awareness and enables precise manipulation of objects.
Miniaturization and Cost Reduction: Miniaturized sensors and advancements in manufacturing processes have made sensors more affordable and accessible, facilitating their widespread adoption in robotic systems.
Cloud Computing and Connectivity
Remote Monitoring and Control: Cloud-based platforms enable real-time monitoring and control of robotic systems from anywhere with an internet connection, improving operational visibility and efficiency.
Data Analytics and Predictive Maintenance: Cloud computing allows for the collection and analysis of large volumes of data generated by robotic systems, enabling predictive maintenance and optimization of performance.
Collaborative Robotics (Cobots)
Safety-Critical Applications: Innovations in collaborative robotics enable robots to work alongside human operators safely, without the need for physical barriers or safety cages.
Ease of Programming and Integration: Cobots are designed to be intuitive to program and easy to integrate into existing workflows, allowing for rapid deployment in diverse applications.
Modular Design and Customization
Interchangeable End-Effectors: Modular robotic systems allow for quick and easy interchangeability of end-effectors, enabling robots to perform a wide range of tasks with minimal reconfiguration.
Scalability and Flexibility: Modular designs facilitate the scalability and customization of robotic systems to meet the specific needs of different industries and applications.